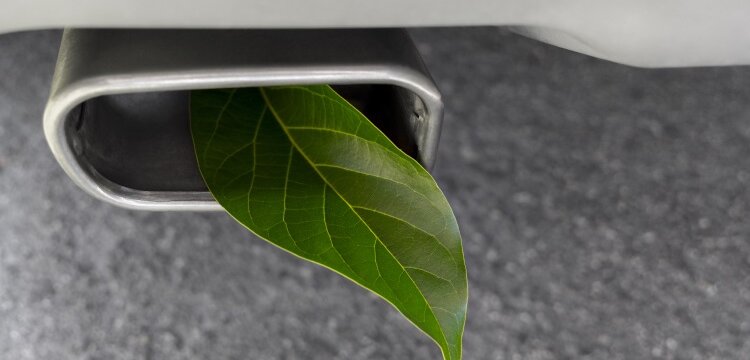
05/10/2020 | Story
Road to 95 – How is it possible to reduce CO2 emissions of cars from 130g to 95g? Rheinmetall offers answers to that question.
There is not just one single product that helps to implement the strict requirements of the European Parliament regarding the reduction of CO2 emissions. On the contrary, Rheinmetall has demonstrated in numerous applications that a large number of different components can independently realise additional savings potential. The basic prerequisites for this are, among other things, a reduction in frictional power or reduced energy absorption.
The general situation is complicated by a new test procedure: The "World Harmonized Light-Duty Vehicle Test Procedure" (WLTP) has been in force in the European Union since September 2017 and applies to passenger cars and light commercial vehicles. It is a globally standardised light vehicle test procedure for determining pollutant and CO2 emissions.
Conditions of the WLTP test procedure
The new procedure is intended to reflect more closely the real operating conditions in road traffic. For example, unlike in the previous "New European Driving Cycle" (NEDC) test programme, fuel consumption is measured at times at a top speed of 130 instead of 120 kilometres per hour and at an ambient temperature of 23 instead of 30 degrees. A large number of new conditions place more stringent demands on developers.
The Rheinmetall mission: Road to 95
"For the established internal combustion engine drive concepts of car manufacturers, Rheinmetall has developed products to help enhance both mechanical and thermodynamic efficiency," emphasises Dipl.-Ing. Heinrich Dismon, Head of Research and Technology at Rheinmetall Automotive.
Rheinmetall relies, among other things, on various systems for exhaust gas recirculation. Originally developed to avoid nitrogen oxides in diesel engines, exhaust gas recirculation is now gaining importance – especially in petrol engines – in order to reduce fuel consumption and CO2 emissions. It is used in high and low pressure versions or with additional efficient cooling of the exhaust gas.
However, friction-optimised coated pistons and bearings made of different materials, valves for controlling the exhaust gas turbocharger or the sector of lightweight construction made from aluminium alloys are also among the top performers in the fight against CO2 emissions.
Emission saving potential exhausted by downsizing the basic engine?
Mega trend: Demand-oriented systems
A high savings potential can be achieved independently of this using demand-oriented systems that only work when they are really needed in engine operation. These include, for example, controllable and adjustable pumps for coolant, oil or the vacuum supply of the brake system.
Another mega trend is the variable control of the valve train. On the one hand, it enables considerable fuel savings. On the other hand, the purely mechanical system developed by Rheinmetall can also switch off entire cylinders when they are not needed – for example in stop-and-go traffic. The variable control of the valve train is a part of the UpValve control system. Watch the animation on how the systems work together: