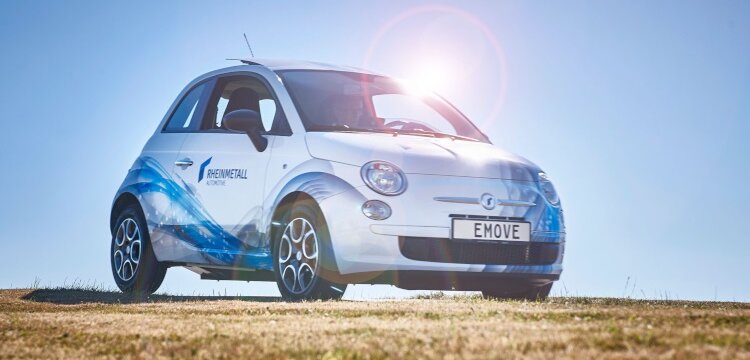
25/08/2020 | Story
Protection tray – Rheinmetall Automotive and Rheinmetall Defence have developed a battery protection tray for underfloor batteries for electric cars
In the Electric Mobility Vehicle (EMove) demo vehicle, based on a Fiat 500, Rheinmetall is showcasing its portfolio in the field of e-mobility.
"Underfloor batteries only have a minor effect on the load volume," says Dr. Peter Seggewiß, Vice President New Automotive Technologies. "They do not shift the vehicle's centre of gravity upwards and offer the option of being installed in the load-bearing vehicle structure," Dr. Seggewiß continues.
In general, in line with the design of the underfloor battery, the energy storage of an electric car is in a crash-safe area. However, the battery in the underbody is initially open and requires additional protection. If, for example, metallic bodies lying on the road are thrown up, the battery cell could be damaged.
To prevent this from happening, Rheinmetall's two corporate sectors Automotive and Defence have together developed a protective shell.
The protection tray developed in partnership: Automotive and Defence coming together
About the battery protection tray
The protection tray for the underbody of the battery consists of a load-adapted fibre composite structure (CFRP/AFRP), which has been tested in extensive impact tests and numerical analyses. "Weighing 14 kilograms, the intrusion protection is about 56 percent lighter than a comparable structure made of aluminium," Dr. Seggewiß continued. In practice, this means that the underbody protection provides dielectric strength against blunt and sharp objects that can hit the battery at speeds of up to 150 km/h without damaging the battery floor. In addition, the battery floor is protected from static load when the vehicle is set down.
The battery pack cover, like the battery protection tray, is also made of fibre composite material. If, for example, a battery fire were to break out, this structure would keep high temperatures away from the passenger compartment. This guarantees an evacuation time of 15 minutes.
By using a material with low thermal conductivity, a flame-retardant plastic matrix as well as an additionally applied thermal protection layer, the battery pack cover meets the high thermal requirements.