
11/09/2024 | Press release
Rheinmetall at Automechanika 2024: Innovations from the Power Systems Division
At the Rheinmetall Group, the Power Systems Division is the hub for innovation and expertise in terms of civilian business. This is where pioneering solutions, control technologies, and digital applications are devised, including for the automotive and energy sectors. In recent months, the Group has revealed some highly promising new developments in this area.
Space-saving kerb-level charging points
The technology group has developed a novel charging solution concept for electric vehicles, which is currently being tested in two pilot projects in Germany. Since April 2024, Rheinmetall kerb-level charging points have been trialled in public places in Cologne and Nörvenich. The kerb-level charging points blend into the urban landscape almost invisibly and provide ways of dealing with the challenges associated with existing charging systems. These include the considerable space they take up, the low density of charging points, the negative impact on the urban landscape, and high costs. Unlike other charging solutions on the market, the Rheinmetall development relies on intelligent use of existing urban infrastructure. The charging electronics, which are tested in accordance with calibration law, are integrated into a kerb and effectively turn it onto a ‘charging column’. So electric vehicles can be charged right next to the kerb, with no need to run lengthy cables across pavements.
At the development stage, great emphasis was placed on easy retrofitting and maintenance. It is possible therefore to prepare whole sections of streets or car parks for the integration of kerb-level charging points and facilitate subsequent scalability. So-called dummy kerb stones are installed for this purpose at the locations where charging points are expected to follow. The electronics module is subsequently added (i.e. retrofitted) once local demand is sufficiently high, due to electromobility gaining ground. The retrofitting process only takes a few minutes – as does maintenance, with the electronics unit being easy to replace, and any downtime likely to be a matter of minutes too. The systems are also designed to reflect environmental conditions at the roadside and thereby ensure a long service life.
Forward-looking technologies in Hartha
In March 2024, at the site operated by Rheinmetall subsidiary Pierburg Pump Technology GmbH in Hartha (Germany), a new manufacturing hall was erected for the production of novel DC-link capacitors. These are superior to the technologies commonly available on the market on account of their electrical properties and temperature stability. At the heart of these innovative capacitors are nano-layer units made of plastic and aluminium, which will also be made on site in future. It is a case of developing completely new technologies, as the special, high-vacuum chemical process and a product with layers a thousandth of a millimetre thick present very great challenges. A close relationship with other sites is also required, as well as with experts from the joint venture partner Polycharge in the USA and with machinery manufacturers. Once the current sample production run is complete, this production line is expected to unlock the site's future. Because the capacitor has the potential to herald a whole new era in the electrification of the vehicle and industrial market. The ultimate aim of the technology is to improve the performance and reliability of capacitors: capacity and energy density are to be increased, with components becoming more compact and temperature-resistant and also lighter and cheaper.
In the years to come, Rheinmetall is planning to make further investments worth around EUR 31 million in the plant at Hartha in order to safeguard production. Including for times when the automotive industry is shifting towards modern, sustainable drive types – and also for ‘beyond automotive’ applications in the industrial sector. The hydrogen recirculation blower (HRB) and the CWA 2000 high-voltage coolant pump for fuel cell applications are other highlights of the modern product range, which also offers potential ‘beyond automotive’ applications. Other strategic goals for securing sustainable success include tapping into new areas with future potential, such as hydrogen technology and achieving CO2 neutrality in production by 2035.
Significant order in mobility area
Electric coolant pump and exhaust gas technology for hybrid vehicles
In June, Rheinmetall announced a major order from a well-known international automotive manufacturer for several million electric coolant pumps. The pump will be used in the manufacturer's hybrid vehicles. Production has already begun and will run until 2030. The pumps can be used in both electric and hybrid applications. They have a compact design and are available in a range of power levels from 50 to 2000 watts.
In July 2024, the subsidiary Pierburg China received two orders in the area of exhaust gas technology for hybrid vehicles. One of them, from a Chinese supplier of carbon canisters, is to provide fuel tank isolation valves (FTIV). The order will run for five years and its total value is in the double-digit millions range. The fuel tank isolation valve plays a key role in plug-in hybrid vehicles as it prevents fuel vapour from escaping and controls the pressure levels in the fuel tank when the vehicle is being driven in electric mode. It is compact, responds quickly, and uses little power. In keeping with the principle of ‘local for local’, Rheinmetall will be setting up a new production line for this order at the Pierburg plant in Kunshan, with a view to starting serial production in January 2026.
The other order was for low-pressure exhaust gas recirculation (LP EGR) valves from another premium Chinese OEM. The value of this order is also in the double-digit millions range and involves the manufacturer's premium limousine and SUV models. The valves are also being made at the Pierburg plant in Kunshan. Serial production is due to start in December 2025, with the contract set to run for six years. Low-pressure exhaust gas recirculation valves reduce nitrogen oxide emissions and fuel consumption. The compact flap-type valve impressed the customer with its various quality features, including high mechanical strength, a long service life, good corrosion resistance, and high positioning accuracy.
High-voltage coolant pumps for electric trucks
A few months earlier, a significant new order was secured in the electric trucks segment involving a six-figure volume of electric high-voltage coolant pumps (CWA 2000). The customer is a world-renowned automotive manufacturer. The order was for high-voltage pumps for use in an electric 800 V architecture. These are designed as wet-running pumps and – in combination with bearings made from a special material optimised for coolant applications – are practically wear-free. The order also includes the supply of replacement parts. Production is scheduled to start in 2025, with supplies to follow over six years until 2030. The technology group managed to win this order in the face of competition from other well-known rivals. The order also paves the way for developing customer relationships in the area of fuel cell applications.
Hydrogen solution in the bus and truck segment
Another new order, in the mid double-digit millions range (EUR), was secured for more than 150,000 HRB 1800 hydrogen recirculation blowers. Following detailed testing of the technology, the customer was convinced the blowers offered the highest quality and robustness currently available on the market. For the subsidiary Pierburg, this marks a milestone in this innovative technology development for fuel cell systems, with the customer placing an order for serial production after the initial provision of samples. Production of the HRB 1800, as ordered, will begin in 2026 and finish five years later in 2030. It will be used in the bus and trucks segment.
By recirculating into the fuel cell stack any unused hydrogen from the reaction in the cell, the hydrogen recirculation blower performs a key function in the fuel cell system as a whole. This increases the efficiency of the fuel cell and extends its service life. In addition, the even distribution of hydrogen in the stack improves the system’s behaviour on starting.
The hydrogen recirculation blower is a so-called balance-of-plant (BoP) product, i.e. one of the components that supply media to the fuel cell stack. On the back of recent successes and with the market expected to pick up, the Group has further stepped up its development efforts for BoP products. A series of innovative components are currently under development. The intention is to gradually extend the range.
The Rheinmetall Group wants to help industry make a sustainable transition – in both automotive and stationary applications – from the combustion engine to modern, environmentally friendly drive types. Rheinmetall is aiming to be climate-neutral by 2035.
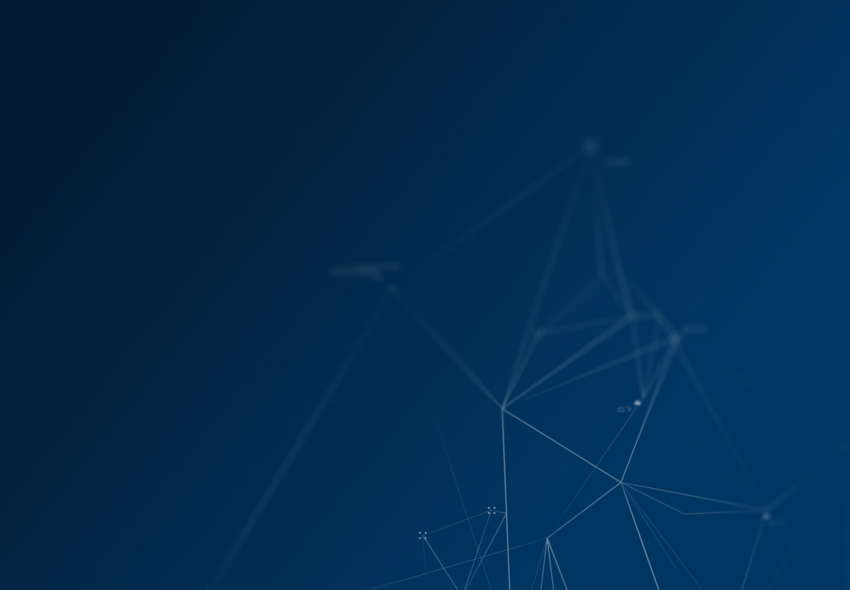